强强联合!PMT携手博格华纳共促汽车产业纵深发展
引言
随着全球气候与环境的极速变化,汽车技术已朝着更节能、更洁净的方向进行转型。能否快速有效地普及新能源技术并推向市场,不仅要依靠强大的研发集成系统,同时也要保证加工生产的高效性。
战略合作启航
博格华纳在动力系统核心部件采购立项阶段,即面向全球启动精密测量合作伙伴遴选。PMT技术团队通过定向技术推介,与博格华纳工程部门建立起专业对话通道。通过现场沟通,PMT团队用ALPHA关节臂对测试设备主轴同轴度不定期的保持监测,并做相应调整,保证装配传动轴质量的稳定性;并对批量的差速器,扭矩矢量系统等工装尺寸进行检测、调整。
在为期3周的技术验证期内,PMT创新应用ALPHA 6轴关节臂联动测量方案:
✓ 建立主轴同轴度动态监测体系,实时捕捉±0.02mm级偏差;
✓ 开发自适应补偿算法,实现传动系统装配精度的闭环控制;
✓ 完成差速器总成、扭矩矢量模块等关键工装的工艺认证;
✓ 搭建过程控制流程,确保量产一致性达99.7%以上。
整个项目历时一个多月,PMT ALPHA关节臂凭借着自身的高精度(±0.02mm级测量精度)、稳定性(72小时连续作业)、超长续航功能以及等臂长设计等特点,赢得了客户的信赖,最终实现M-2.5m型号的成功交付,为传动系统智能制造树立行业新标杆。
关于博格华纳
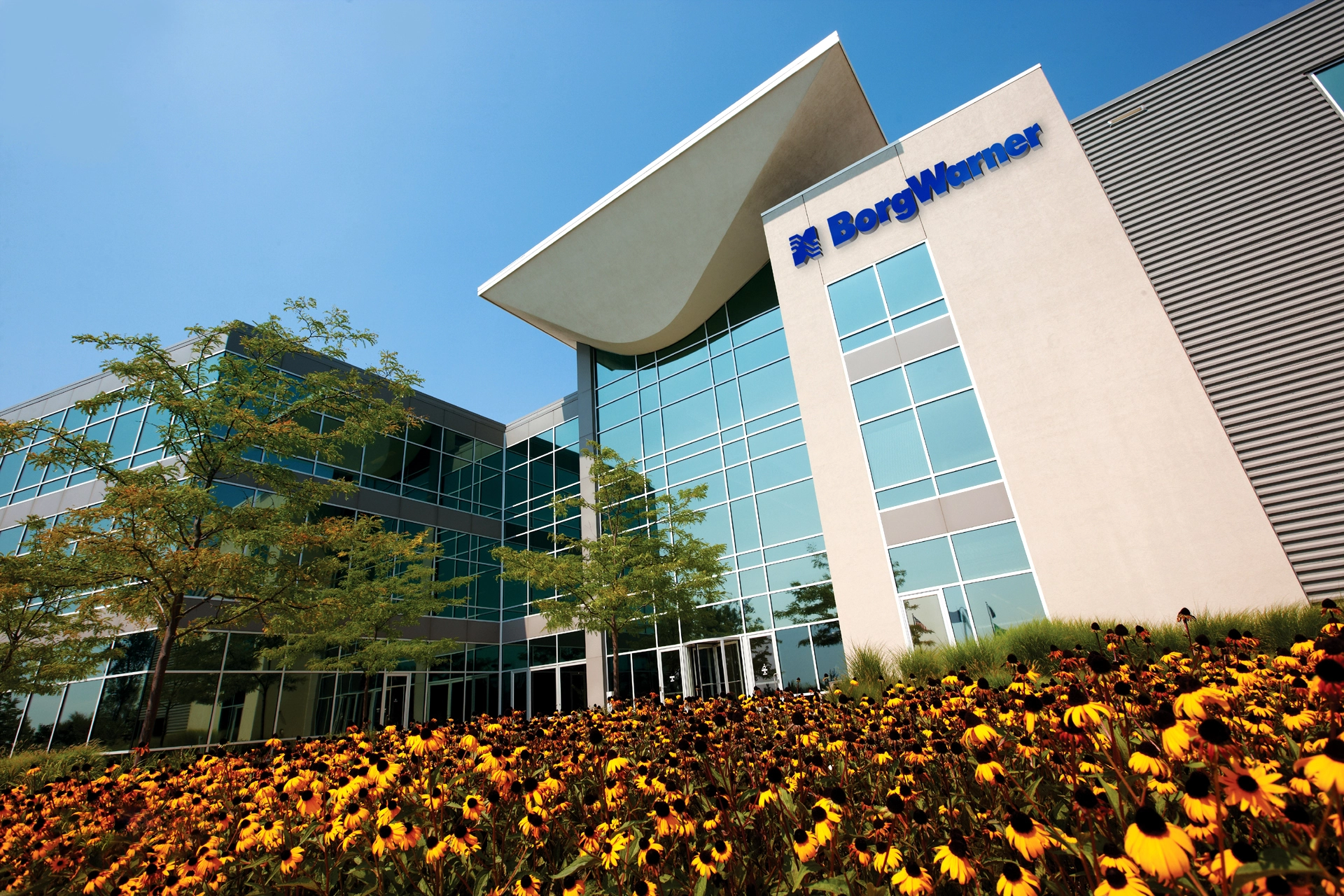
高效解决方案解析
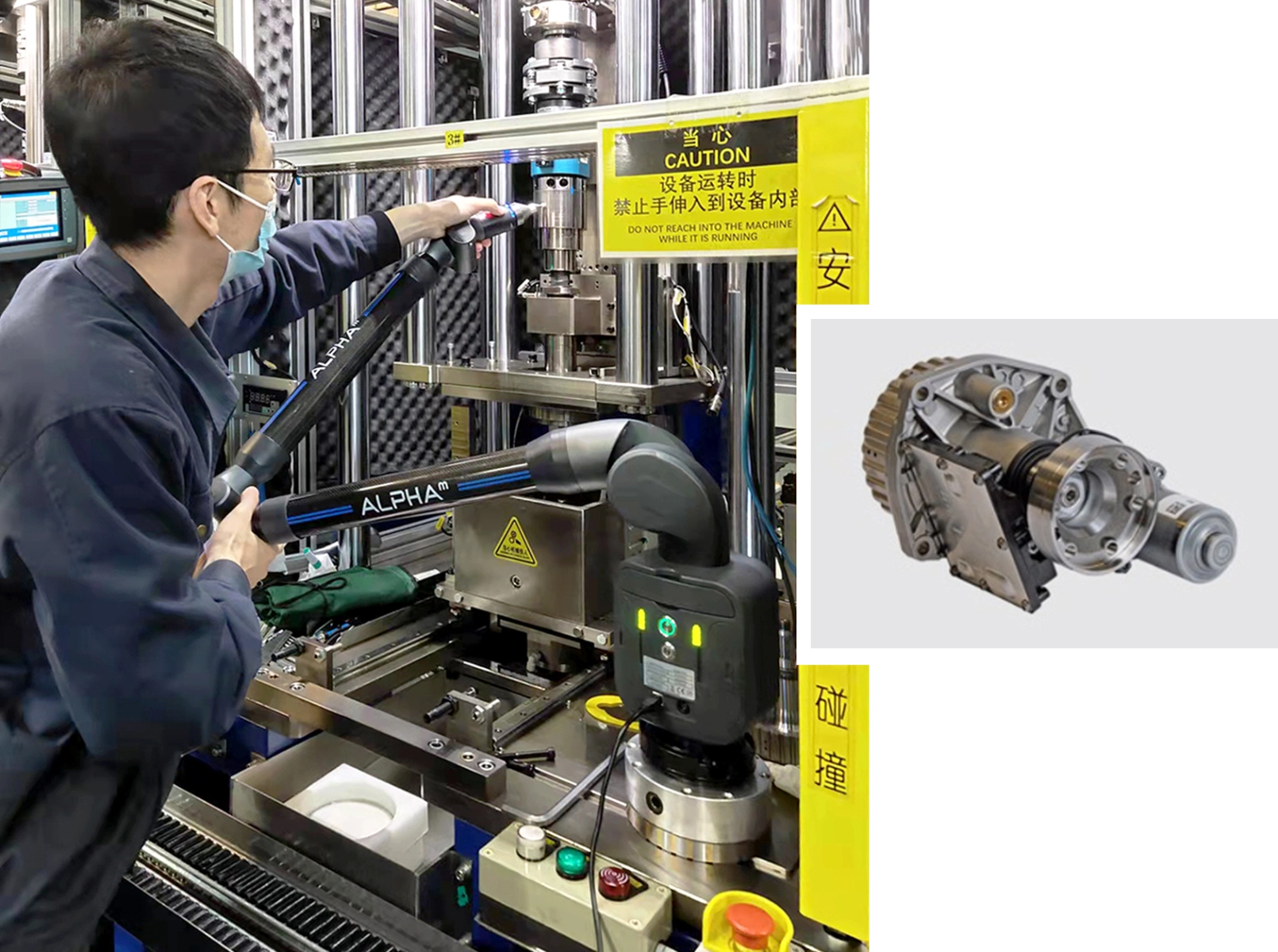
未来展望
在全球汽车产业向”新四化”深度转型的关键阶段,整车技术突破正加速重构供应链生态体系。作为驱动系统创新标杆企业,博格华纳依托PMT在精密测量领域的核心技术与数字解决方案,双方已形成从工艺验证到量产优化的技术闭环,以数据驱动的智能检测体系赋能制造端实现99.96%的过程良率,共同推进汽车产业价值链条向高效化、数字化、可持续方向进化,为全球车企的电动化转型提供底层技术支撑。